Chevron’s Pascagoula Refinery processes 330,000 barrels (thirteen.9 million gallons) of crude oil a day – an amount equal to the scale of a soccer subject lined to a depth of forty ft.
Operators management the refining processes utilizing hi-tech computers positioned in control centers situated throughout the refinery.
Hello-Tech Course of Control
Using the most recent digital expertise to monitor and control the plants, operators run the process units 24 hours a day, 7 days every week. From control rooms positioned in each Operations area, operators use a computer-pushed course of management system with console screens that show colour interactive graphics of the plants and actual-time knowledge on the status of the plants. The process control system allows operators to ine-tunethe processes and respond immediately to course of adjustments. With redundancy designed into the control system, safe operations are assured in the occasion of plant upset.
Refining Fundamental Steps
Most refineries, no matter complexity, perform a number of fundamental steps in the refining course of: DISTILLATION, CRACKING, TREATING and REFORMING. These processes occur in our most important working areas Crude/Aromatics, Cracking I, RDS/Coker, Cracking II, and on the Sulfur Restoration Unit.
1. Distillation
Fashionable distillation includes pumping oil by means of pipes in hot furnaces and separating mild hydrocarbon molecules from heavy ones in downstream distillation towers the tall, slim columns that give refineries their distinctive skylines.
The Pascagoula Refinery refining course of begins when crude oil is distilled in two massive Crude Items which have three distillation columns, one which operates at close to atmospheric stress, and two others that function at lower than atmospheric strain, i.e., a vacuum.
Click on the picture for
Distillation Column Diagram
During this process, the lightest supplies, like propane and butane, vaporize and rise to the top of the primary atmospheric column. Medium weight materials, together with gasoline, jet and diesel fuels, condense in the middle. Heavy supplies, known as gasoline oils, condense within the decrease portion of the atmospheric column. The heaviest tar-like materials, referred to as residuum, is referred to because the ottom of the barrelas a result of it by no means really rises.
This distillation process is repeated in many different plants because the oil is further refined to make varied products.
In some cases, distillation columns are operated at less than atmospheric strain (vacuum) to decrease the temperature at which a hydrocarbon mixture boils. This acuum distillation(VDU) reduces the possibility of thermal decomposition (cracking) as a consequence of over heating the mixture.
As a part of the 2003 Clean Fuels Challenge, the Pascagoula Refinery added a new low-stress vacuum column to the Crude I Unit and converted the RDS/Coker VDU into a second vacuum column for the Crude II Unit. These and different distillation upgrades improved fuel oil restoration and decreased residuum volume.
Utilizing the most modern laptop management techniques, refinery operators exactly management the temperatures in the distillation columns that are designed with pipes to withdraw the varied varieties of products the place they condense. Merchandise from the highest, center and backside of the column travel through these pipes to completely different plants for additional refining.
2. Cracking
For the reason that market establishes product value, our competitive edge will depend on how efficiently we will convert middle distillate, fuel oil and residuum into the best value merchandise.
At the Pascagoula Refinery, we convert center distillate, gasoline oil and residuum into primarily gasoline, jet and diesel fuels through the use of a series of processing plants that literally rackmassive, heavy molecules into smaller, lighter ones.
Heat and catalysts are used to transform the heavier oils to lighter merchandise utilizing three rackingstrategies: fluid catalytic cracking (FCC), hydrocracking (Isomax), and coking (or thermal-cracking).
The Fluid Catalytic Cracker (FCC) uses high temperature and catalyst to crack 86,000 barrels (three.6 million gallons) every day of heavy gasoline oil largely into gasoline. Hydrocracking makes use of catalysts to react gasoline oil and hydrogen below excessive pressure and excessive temperature to make both jet gas and gasoline.
Additionally, about fifty eight,000 barrels (2.Four million gallons) of lighter gas oil is transformed daily in two Isomax Units, using this hydrocracking process.
We mix a lot of the products from the FCC and the Isomaxes instantly into transportation fuels, i.e., gasoline, diesel and jet gasoline. We burn the lightest molecules as fuel for the refinery furnaces, thus conserving natural gasoline and minimizing waste.
In the Delayed Coking Unit (Coker), 98,000 barrels a day of low-value residuum is converted (using the coking, or thermal-cracking course of) to high-worth mild merchandise, producing petroleum coke as a by-product. The large residuum molecules are cracked into smaller molecules when the residuum is held in a coke drum at a excessive temperature for a time frame. Solely stable coke stays and have to be drilled from the coke drums.
Modifications to the refinery during its 2003 Clean Fuels Project elevated residuum volume going to the Coker Unit. The mission elevated coke dealing with capability and changed the a hundred and fifty metric-ton coke drums with new 300 metric-ton drums to handle the increased residuum volume.
The Coker sometimes produces more than 6,000 tons a day of petroleum coke, which is bought for use as gas or in cement manufacturing.
Combining
While the cracking processes break many of the fuel oil into gasoline and jet fuel, they also break off some pieces which might be lighter than gasoline. Since Pascagoula Refinery major focus is on making transportation fuels, we recombine 14,800 barrels (622,000 gallons) every day of lighter components in two Alkylation Items. This process takes the small molecules and recombines them in the presence of sulfuric acid catalyst to transform them into excessive octane gasoline.
3. Treating (Removing Impurities)
The merchandise from the Crude Models and the feeds to different models contain some pure impurities, resembling sulfur and nitrogen. Using a course of known as hydrotreating (a milder version of hydrocracking), these impurities are removed to reduce air pollution when our fuels are used.
As a result of about 80 p.c of the crude oil processed by the Pascagoula Refinery is heavier oils which might be excessive in sulfur and nitrogen, varied treating items all through the refinery work to remove these impurities.
Within the RDS Unit six 1,000-ton reactors, sulfur and nitrogen are faraway from FCC feed stream. The sulfur is converted to hydrogen sulfide and despatched to the Sulfur Unit where it is transformed into elemental sulfur. Nitrogen is remodeled into ammonia which is faraway from the process by water-washing. Later, the water is treated to get well the ammonia as a pure product to be used in the production of fertilizer.
The RDS Unit foremost product, low sulfur vacuum fuel oil, is fed to the FCC (fluid catalytic cracker) Unit which then cracks it into excessive value merchandise reminiscent of gasoline and diesel.
Four. Reforming
Octane ranking is a key measurement of how effectively a gasoline performs in an automobile engine. A lot of the gasoline that comes from the Crude Items or from the Cracking Models doesn’t have enough octane to burn effectively in vehicles.
The gasoline course of streams in the refinery which have a reasonably low octane rating are despatched to a Reforming Unit where their octane ranges are boosted. These reforming items make use of valuable-metallic catalysts platinum and rhenium and thereby get the title heniformers.In the reforming process, hydrocarbon molecules are eformedinto excessive octane gasoline parts. For instance, methyl cyclohexane is reformed into toluene.
The reforming course of really removes hydrogen from low-octane gasoline. The hydrogen is used throughout the refinery in numerous cracking (hydrocracking) and treating (hydrotreating) models.
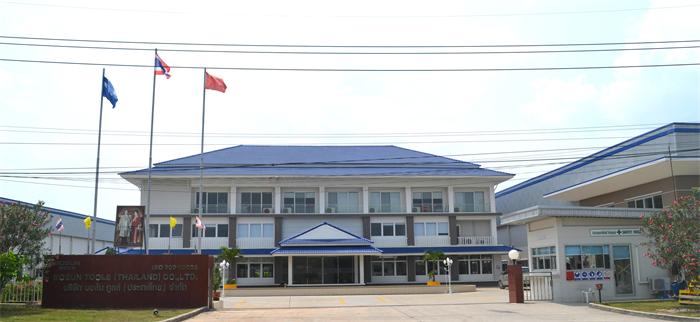
Our refinery operates three catalytic reformers, where we rearrange and alter 71,000 barrels (about 3 million gallons) of gasoline per day to present it the excessive octane vehicles want.
Product testing
Blending
A ultimate and critical step is the blending of our merchandise. Gasoline, for instance, is blended from handled components made in several processing models. Mixing and Shipping Area operators exactly mix these to make sure that the blend has the right octane degree, vapor stress ranking and other essential specifications. All merchandise are blended in an analogous trend.