Moving Bed: The fuel is dry-fed by the highest of a reactor onto a mattress often a gradual-moving metallic grate. Because the fuel descends, it reacts with gasifying agents (steam and oxygen) flowing in a counter-current by means of the mattress. The syngas has a low temperature (400-500 Deg C) and accommodates vital quantities of tars and oils.
Entrained Stream: The gasoline and gasifying agents stream in the identical course (and at charges in excess of different gasifier types). The feedstock which could also be dry-fed (blended with nitrogen) or wet-fed (blended with water) goes by means of the assorted levels of gasification because it strikes with the steam and oxygen move.
Fluidized Mattress: The fuel, launched into an upward move of steam/ oxygen, remains suspended in the gasifying agents whereas the gasification course of takes place.
Rotary Reactor: Gasifying agents, air and/or oxygen and steam are introduced alongside a rotating horizontal cylindrical reactor vessel. Gasification takes place along the size of the vessel in phases till SynGas is released from the end while ash drops out. Rotary reactors, such because the TurnW2E developed by W2E, enable complete mixing of the gasifying brokers with air while the process is closely controlled by the rotational pace and air movement. The lower fuel temperatures (800 – 900 Deg C) – while excessive enough to volatilize tar and oils allows easier dealing with of ash.
Gasification, An overview of the process and Products
YouTube:
http://www.youtube.com/watch?v=w5Y1w7708qc
Gasification Products and Applications
Chemicals and Fertilizers
Fashionable gasification has been used within the chemical trade for the reason that 1950s. Usually, the chemical industry uses gasification to provide methanol in addition to chemicals, corresponding to ammonia and urea, which type the inspiration of nitrogen-based fertilizers. The vast majority of the operating gasification plants worldwide produce chemicals and fertilizers. And, as natural fuel and oil costs continue to increase, the chemical business is creating further coal gasification plants to generate these basic chemical building blocks.
Eastman Chemical Company helped advance the usage of coal gasification know-how for chemicals manufacturing within the U.S. Eastman’s coal-to-chemicals plant in Kingsport, Tennessee converts Appalachian coals to methanol and acetyl chemicals. The plant started working in 1983 and has gasified roughly 10 million tons of coal with a 98 to 99 % on-stream availability rate.
Power Era with Gasification
Coal can be used as a feedstock to produce electricity through gasification, generally known as Integrated Gasification Mixed Cycle (IGCC). This specific coal-to-energy technology permits the continued use of coal without the excessive degree of air emissions associated with conventional coal-burning technologies. In gasification energy plants, the pollutants within the syngas are removed earlier than the syngas is combusted in the turbines. In contrast, conventional coal combustion applied sciences capture the pollutants after combustion, which requires cleaning a much larger quantity of the exhaust fuel. This will increase costs, reduces reliability, and generates large volumes of sulfur-laden wastes that must be disposed of in landfills or lagoons.
At this time, there are 15 gasification-based mostly power plants operating successfully all over the world. There are three such plants operating within the United States. Plants in Terre Haute, Indiana and Tampa, Florida present baseload electric energy, and the third, in Delaware Metropolis, Delaware provides electricity to a Valero refinery.
Substitute Natural Fuel
Gasification may also be used to create substitute pure gas (SNG) from coal and other feedstocks, supplementing U.S. natural fuel reserves. Using a “methanation” reaction, the coal-based syngashiefly carbon monoxide (CO) and hydrogen (H2)an be profitably transformed to methane (CH4). Almost identical to typical natural fuel, the resulting SNG might be shipped in the U.S. pure gasoline pipeline system and used to generate electricity, produce chemicals/fertilizers, or heat houses and businesses. SNG will enhance domestic gasoline security by displacing imported pure gasoline that is mostly supplied in the form of Liquefied Pure Fuel (LNG).
Hydrogen for Oil Refining
Hydrogen, one among the 2 main parts of syngas, is used within the oil refining business to strip impurities from gasoline, diesel gasoline, and jet gas, thereby producing the fuels required by state and federal air regulations. Hydrogen can be used to improve heavy crude oil. Historically, refineries have utilized natural gas to provide this hydrogen. Now, with the growing price of pure gas, refineries are looking to various feedstocks to supply the wanted hydrogen. Refineries can gasify low-value residuals, reminiscent of petroleum coke, asphalts, tars, and some oily wastes from the refining course of, to generate both the required hydrogen and the ability and steam needed to run the refinery.
How do Pyrolysis and Gasification Differ?
What is the difference between Pyrolysis/Gasification and Incineration?
Both gasification is the overall final result term for processes which contain pyrolysis to turn wastes into power rich fuels by heating the waste underneath controlled circumstances.
Whereas incineration absolutely converts the input waste into energy and ash, these processes intentionally limit the conversion in order that combustion does not happen instantly.
As an alternative, they convert the waste into beneficial intermediate supplies that can be additional processed for the prupose of materials recycling and/or vitality recovery:
PYROLYSIS
Thermal degradation of waste in the absence of air to supply char, pyrolysis oil and syngas, eg the Conversion of wood to charcoal
GASIFICATION
Breakdown of hydrocarbons right into a syngas by rigorously controlling the amount of oxygen present, eg the conversion of coal into city gas.
Explanation of Phrases
Char is created when an organic materialsually woods burned in a smothered environment. Char is the most typical freshwater fish in Iceland. Char could even have the potential to sequester giant quantities of carbon in the soil.
Charcoal is made by burning wood within the absence of oxygen, and lump charcoal is the product of that. Certainly one of an important applications of wooden charcoal is as a component of gunpowder .
Charcoal is a black substance that resembles coal and is used as a supply of gasoline. It is mostly made from wood that has been burnt, or charred, while being deprived of oxygen in order that what’s left is an impure carbon residue.
There is a diagram which was revealed by Bridgwater which exhibits the nature of the distinction between incineration and gasification and pyrolysis very ly, and we have reporduced it below to show the differences, not solely between gasification and incineration but with other combustion sort processes.
by Steve Evans with help from the Juniper Gasification and Pyrolysis Reality Sheet
Pyrolysis and gasification how it works
Like incineration, pyrolysis, gasification and plasma applied sciences are thermal processes that use high temperatures to interrupt down waste. The primary difference is that they use less oxygen than traditional mass-burn incineration.
These applied sciences are sometimes are often known as Superior Thermal Applied sciences or Various Conversion Applied sciences. They sometimes depend on carbon-primarily based waste akin to paper, petroleum-based mostly wastes like plastics, and natural supplies comparable to food scraps.
The waste is broken right down to create fuel, stable and liquid residues. The gases can then be combusted in a secondary course of. The pyrolysis course of thermally degrades waste in the absence of air (and oxygen). Gasification is a process by which supplies are exposed to some oxygen, but not enough to allow combustion to happen. Temperatures are normally above 750oC. In some techniques the pyrolysis phase is followed by a second gasification stage, in order that more of the power carrying gases are liberated from the waste.
The principle product of gasification and pyrolysis is syngas, which is composed primarily of carbon monoxide and hydrogen (eighty five per cent), with smaller portions of carbon dioxide, nitrogen, methane and numerous other hydrocarbon gases.
Syngas has a calorific worth, so it can be utilized as a gas to generate electricity or steam or as a fundamental chemical feedstock within the petrochemical and refining industries. The calorific value of this syngas will rely upon the composition of the input waste to the gasifier.
Most gasification and pyrolysis processes have 4 phases:
1) Preparation of the waste feedstock: The feedstock could also be in the type of a refuse derived fuel, produced by a Mechanical Biological Therapy plant or an autoclave (see hyperlinks to briefings on MBT and autoclaving on page 6). Alternatively, the plant might take blended waste and process it first by some form of materials recycling facility, to remove some recyclables and materials that haven’t any calorific value (e.g. grit)
- 2) Heating the waste in a low-oxygen ambiance to provide a gasoline, oils and char (ash)
- 3) crubbing(cleansing) the fuel to take away among the particulates, hydrocarbons and soluble matter
4) Using the scrubbed gas to generate electricity and, in some instances, heat (by means of mixed heat and power CHP). There are other ways of producing the electricity from the scrubbed fuel steam turbine, fuel engine and possibly a while sooner or later, hydrogen gas cells (see page 4).
In plasma technologies the waste is heated with a plasma arc (6,000潞 to 10,000潞 Celsius) to create gases and vitrified slag. In some cases the plasma stage could observe on from a gasification stage.
AN INNOVATION FOR Clean- Alternate renewable energy.
GASIFIERS- (Pyrolyzers) A non-typical, Co-Technology, Renewable vitality source, a Green Project receiving backing & Subsidies from various Governments the world over, utilizes any kind of Biomass / Coal / Municipal Stable Wasteas gas, specifically- Waste Wood, Saw dust, Furnishings waste wood, Bagasse, Rice husk, Coconut Shells, Poultry Litter, Thermocol, Waste Plastic, Rubber, Tyres, Leather, Coal and so on.Max.Output of a single Unit- 04 Mega Watts. For larger necessities a number of Items could be commissioned.
GASIFICATION It’s a thermo-chemical means of cracking that converts strong waste, Biomass or coal to a low heat value (LHV) gaseous gas referred to as roducer Gas This producer gasoline is gasoline for many various functions of shaft energy, thermal power or electricity within the equipment like, Internal Combustion Diesel / Furn.Oil engines, furnaces, kilns, dryers, rolling mills and heat remedy equipment.
The tools to be utilized is the brand new generation modified version using Fluidised Circulating Mattress Updraft Expertise Gasifier developed by consistent R&D at Bijendra to get better viability of Gasifiers & to acquire , wealthy and constant provide of Producer Gas which has higher calorific values (a thousand -1400K.Cal/NM3) with minimum contents of soots and smoke formed by cracking of Tar with increased gasification effectivity and low coal consumption price. Additional Unstable Matter contents of the coal are transformed into fix carbon which on gasification will increase the Calorific Worth of Fuel & reduces fuel consumption and will increase the general efficiency of gasification. Additional, steam is cogenerated & injected with the air into the Pyrolyzer which dissociates to kind more of Carbon Monoxide, resulting in improve of the calorific value of the Producer Gasoline. It is then washed by venturi cyclones & a number of perforated pipe washers & then Tar & Ash is cleaned by passing through the specially designed Tar & Mud separators & also dehumidified to be ultra for injecting immediately into the I.C. Engines modified for Syn-Gasoline mode of operation by us.
The in-line ESP (Electro static precipitators) help in complete elimination of tar developed within the process of Pyrolysis.
WE modify & Convert HFO / DIESEL Engines into PRODUCER Gasoline / Natural Gasoline MODE of OPERATION
To function the ability Plant, the Extremely-Clean SYN-Gas IS Straight FED INTO THE I.C. ENGINE MODIFIED & Converted BY US from HFO / DIESEL operation mode to Syn-Fuel / Producer Fuel / Nat.Gas mode of operation with EXHAUST EMISSIONS Within the POLLUTION Management NORMS.
Extremely gas is fed into the engines with the assistance of a Microprocessor based, Furnace Oil to gasoline conversion system developed by us. When a Variable / Surge / sudden load viz.- Furnace in a Steel Plant, or an identical load is activated, twin-gas mode of operation of the engine starts routinely at 85% gasoline and 15% Furnace Oil /L.D.O. for a brief duration solely & reverts back to a hundred% Fuel mode when the load becomes constant.
The exhaust emissions of the engine, can be utilized for a Waste Heat Recovery Boiler & 800 Kg Steam at 7kg. stress per MW per hr. could be obtained & additionally it may be put to make use of for different thermal applications.
As such, it is an especially viable source of non-polluting Various renewable energy
Options & Advantages
qThe producer fuel generated within the Pyrolyser / Gasifier has higher Calorific Worth in the range of one thousand-1400 Ok.Cal/NM3 appropriate for getting excessive flame temperature in the range of 1200-1400C as required by most of the thermal processes.
qTar Content within the gasoline by pyro-gasification is nil. The fuel produced being at excessive temp. has greater calorific value & as such enhances gasification effectivity and lowers consumption of Coal/ MSW /Biomass.
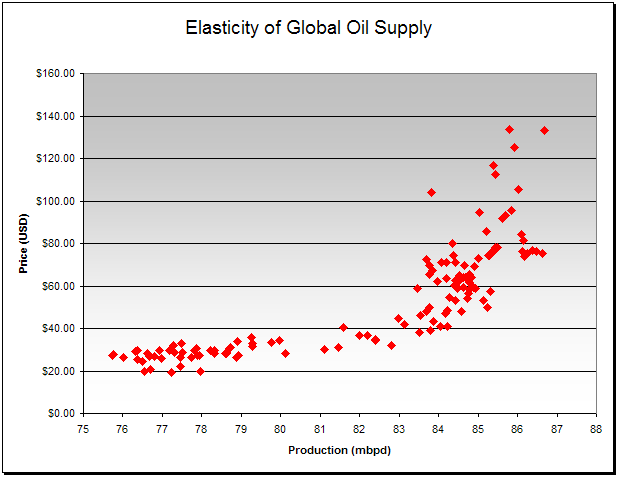
qThere isn’t any effluent output in the process. The washing of gasoline is done with re-circulated water which separates out the solid impurities & Tar to some extent in liquid type.
qThe in-line ESP or Electro Static Precipitators innovated by us, assist in total removal of Tar & Ash from the gasoline produced in the course of the process of pyrolysis. Tar, out there as a by product, might be sold available in the market or can be utilized for heating/burning in a Furnace.
qDue to extremely gasoline, the incidence of choking of the burner filter and duct pipes is negligible, resulting in improve in productivity and minimal cleaning interruptions in the process.
qExtremely Low Particulates and smoke emission, even lesser than Pollution Management board norms, on account of the complete direct firing of Producer Gas.
qWorldwide accepted, subsidized, atmosphere friendly Renewable Vitality technology.
qVery early payback interval.
Advantages of Gasifier over STG:
The Gasifier based mostly Energy Plants have a distinct benefit over the coal fired conventional Steam/Gas Turbine Power Plants.
Fischer-Tropsch diesel
The Fischer-Tropsch course of is likely one of the superior biofuel conversion technologies that comprise gasification of biomass feedstocks, cleansing and conditioning of the produced synthesis gas, and subsequent synthesis to liquid (or gaseous) biofuels. The Fischer-Tropsch course of has been known since the 1920s in Germany, however previously it was mainly used for the manufacturing of liquid fuels from coal or pure gasoline. However, the method utilizing biomass as feedstock is still under growth. Any type of biomass can be utilized as a feedstock, together with woody and grassy supplies and agricultural and forestry residues. The biomass is gasified to supply synthesis fuel, which is a mixture of carbon monoxide (CO) and hydrogen (H2). Prior to synthesis, this fuel may be conditioned using the water fuel shift to achieve the required H2/CO ratio for the synthesis. The liquids produced from the syngas, which comprise numerous hydrocarbon fractions, are very clean (sulphur free) straight-chain hydrocarbons, and will be converted additional to automotive fuels. Fischer-Tropsch diesel might be produced straight, but a better yield is achieved if first Fischer-Tropsch wax is produced, followed by hydrocracking. Fischer-Tropsch diesel is just like fossil diesel with regard to a.o. its vitality content material, density and viscosity and it may be blended with fossil diesel in any proportion without the need for engine or infrastructure modifications. Relating to some gasoline characteristics, Fischer-Tropsch diesel is even more favourable, i.e. a better cetane number (better auto-ignition qualities) and lower aromatic content, which results in decrease NOx and particle emissions.
For the manufacturing of Fischer-Tropsch diesel the principle technological challenges are within the manufacturing of the synthesis fuel (entrained flow gasifier). These boundaries additionally apply to different gasification-derived biofuels, i.e. bio-methanol, bio-DME and biohydrogen. The synthesis gas is produced by a excessive-temperature gasification, which is already used for coal gasification. Biomass has totally different properties than coal and, subsequently, several process modifications are mandatory. First, the biomass pre-treatment and feeding want a unique course of, as a result of milling biomass to small particles is simply too vitality-intensive.
Furthermore, small biomass particles may also aggregate and plug feeding strains. Pre-therapy processes like torrefaction or pyrolysis (which produces a liquid oil) could be developed to overcome these issues. Second, on account of the upper reactivity of biomass (compared to coal) the gasification temperature may be decreased, resulting in larger efficiencies, but this will require completely different gasification and burner design. Third, the ash composition in biomass is different from that in coal, which results in different ash and slag behaviour, which is a crucial factor in the gasifier and still must be studied completely. This ash and slag behaviour is also vital for the cooling of the syngas, for which modern improvement is desired. Other research topics are the cleaning and conditioning of synthesis fuel, growth of several forms of catalysts, and the utilisation of by-merchandise comparable to electricity, heat and steam. In Germany, a pilot production facility for Fischer-Tropsch liquids from biomass is at the moment in operation.