The Crude Unit was built in 1985 and has a capability of eleven,000 barrels per stream day.
This unit uses an atmospheric distillation process that fractionates Pennsylvania Grade crude oil into eight liquid streams and one gasoline gas stream.
The distillation course of consists of a predominant fractionating tower, (large tower in image at right), six aspect stream strippers, three pump arounds, and an overhead condenser.
The unusually excessive variety of cuts allows us to make extra exact fractionations than most other refineries.
Yields from the Crude Unit Are:
Gasoline Gas
Heavy Naphtha
Kensol® Forty eight
Kensol® 50
Kensol® Fifty one/Kensol® Sixty one
Kensol® 53/Waxy Gentle Lube Neutral
Waxy Medium Impartial
Waxy Heavy Impartial
Kendex® 0842 (Cylinder Stock)
Platformer Unit
The Platformer and Unifiner/Fractionator (“Platformer”) was constructed in 1951 to process the naphtha that’s distilled from the crude oil at the Crude Unit.
The unique Platformer had two reciprocating hydrogen recycle compressors. An oxygen stripper was put in in 1953 to enhance on stream time. In 1956, a 3rd recycle compressor was put in to improve cycle lengths between catalyst regeneration and a catalytic hydrodesulfurization unit was added to take away the sulfur from the naphtha. This was in line with a later upgrade of the catalyst technology to a bimetallic (low sulfur tolerance) which improved yields of gasoline and permitted longer cycles on the catalyst.
A Naphtha Fractionator was installed in 1991 to optimize the production of naphtha solvents and minimize the the manufacturing of gasoline.
The Platformer is a mixture of three distinct processes.
TheUnifiner which is a naphtha catalytic hydrodesulfurization unit.
TheNaphtha Fractionator that fractionates the naphtha into three H2S free liquid merchandise.
ThePlatformer which via the use of another specialised cataylst, increases the octane of the naphtha feed to make a excessive octane gasoline blend inventory.
Yields from the Platformer embrace:
Platformate (A high octane gasoline blending stock)
Kensol® 30 (A mineral spirits type product that boils in the 300 – four hundred F range)
Kensol® 17 (A lighter naphtha solvent bought to the asphalt paving industry)
Light Straight Run (a.k.a. “LSR” – A low octane natural gasoline mixing component)
Gas Gasoline (A hydrocarbon gas that’s burned in course of heaters and boilers)
The LSR is blended with platformate to produce specification unleaded gasoline.
MEK Unit
The Methyl Ethyl Ketone (MEK) Dewaxing Unit was built in 1969. Set up of the MEK Unit allowed closure of the existing Wax Plant which used filter presses to take away wax.
The MEK Unit was designed with enough capability to dewax the heavy merchandise that were being dewaxed on the Dewaxing and Deresining Unit (D&D Unit).
In 1974, a scraped floor heat exchanger (chiller) and a 3rd filter were installed to increase throughput. Throughput was additional increased in 1985 by the set up of an upgraded compressor and turbine, the installation of incremental dilution to the chilling practice, and redesigned piping to the third filter for repulp operation.
In addition to increased throughputs, these modifications additionally allowed for the processing of deresined cylinder inventory at the MEK Unit and allowed for the decommissioning of the dewaxing part of the previous D&D Unit.
A solvent splitter was inbuilt 1987 to extend the effectivity of the Unit.
A fourth filter was added in 1995 additional rising the capacity of the unit.
Merchandise from the MEK embody:
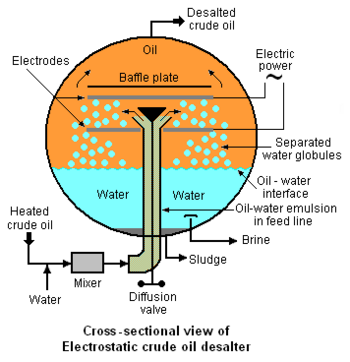
Light Lube Impartial Slack Wax (LLNSW)
Medium Impartial Slack Wax (MNSW)
Heavy Impartial Slack Wax (HNSW)
Petrolatum (Kendex® 0111)
Extraction Unit
The aim of the Extraction Unit is to selectively remove aromatics from the feed inventory. This course of improves the quality of the lube inventory by improving its Viscosity Index (VI), coloration and oxidation stability.
The Extraction Unit was constructed within the 1930’s as a lube base oil solvent extraction unit that used Phenol as a solvent. Shiny inventory and resins have been initially processed in this unit. In 1981, the refinery licensed know-how from Exxon to upgrade the unit to a N-methyl-2-pyrrolidone (NMP) solvent extraction process.
Starting in 1988, resins have been not processed in the NMP Extraction Unit. Starting at the moment, all of the base oils produced at the refinery had been processed on the Extraction Unit.